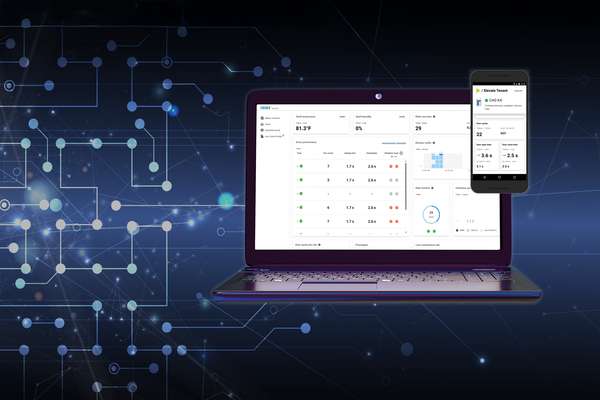
Turning Elevator Sensor Data into Actionable Insights
With the number of units under maintenance increasing and the pool of skilled labor shrinking at the same time, it is crucial to find new ways to optimize elevator maintenance without compromising the quality of service. That’s where the value of elevator sensor data becomes evident. Discover some real-life examples of how CEDES is turning this data into actionable insights through IoT.
IoT Data Backbone: Sensor Fusion
IoT is enabling the transition from corrective and preventive maintenance towards usage-based and predictive maintenance. Previous generations of IoT solutions were based on the elevator controller’s diagnostic data, yet this approach turned out to have some limitations in terms of data accuracy and usability. Capturing data directly at the source, i.e. from elevator sensors, offers truly universal IoT enablement, easy to use in every elevator irrespective of its make, model, or age.
CEDES is known as the manufacturer of the first commercial elevator light curtain. Today, we are adding intelligence to this standard component by equipping it with additional sensors (such as barometers, accelerometers, and thermometers), processing the data from this sensor fusion in a gateway, and making it available through the cloud-based IoT platform CEDES Elevate. From this easy hardware setup, end users get a plethora of insights on elevator health, visualized in a dashboard on any connected device.
The big question is: how can service companies make use of these insights in their daily operations? Early installations demonstrate quick wins, proving the solution’s value in increasing maintenance efficiency and customer satisfaction.
Case in Point: Feedback from the Field
Increased vibration trends are usually a good indicator of potential elevator breakdowns. In a mid-rise multiuse building in New Jersey, an increasing car vibration trend was observed since August last year and by November it became noticeable to residents and users. The technician dispatched was equipped with insights from the CEDES Elevate dashboard, pointing to the floors in which the problem was most acute.
Door issues are the leading cause of elevator breakdowns and generate anywhere between 60 to 80% of service callbacks. Therefore, measuring door performance is key to guiding targeted maintenance actions to improve equipment health and availability. In this case, a spike in car door vibration along with door closing times of over 4 seconds, out of the norm for that particular elevator, were identified. A technician was dispatched to check the car door on the third floor based on data from CEDES Elevate, where they found that the door operator bolts to the linkage arm had become loose. A quick change of hardware and proper tightening allowed for the issue to be resolved, and the elevator was kept in service. The building facilities team had no knowledge of the issue and were glad that the elevator company was able to act quickly and save a potential shutdown before it occurred.
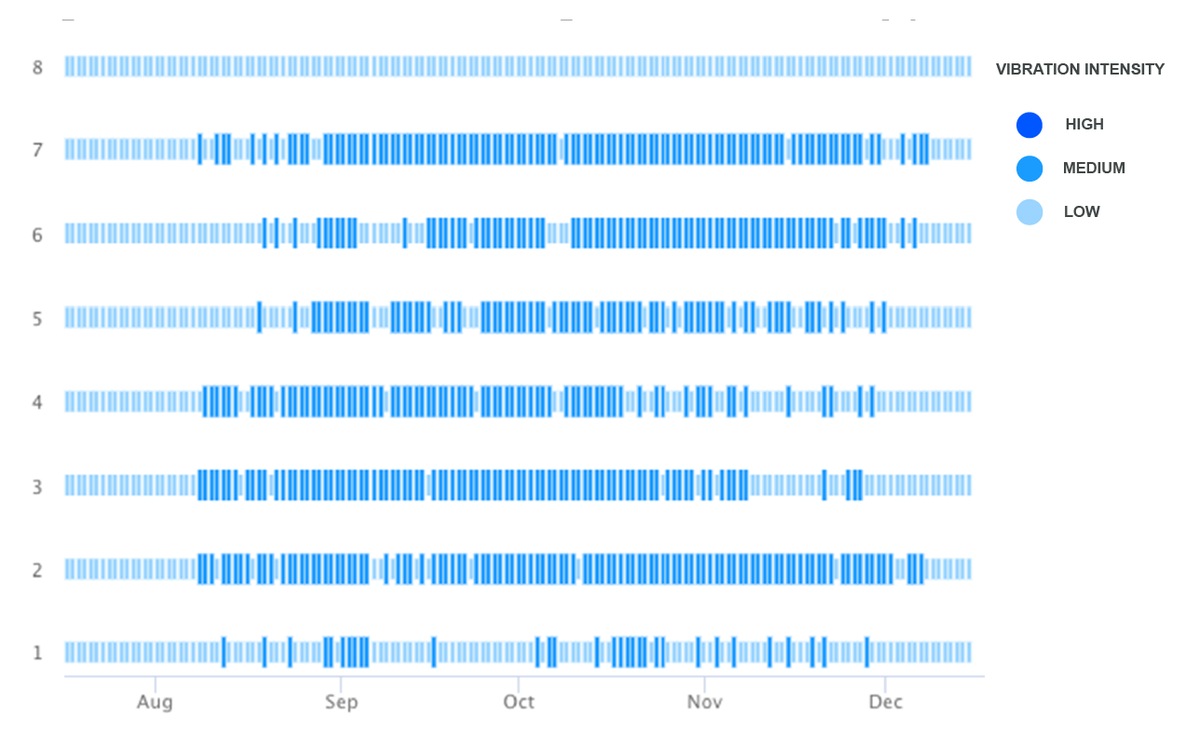
This allowed them to quickly locate the issue and identify the root cause in worn-out elevator car guide rollers. The parts were replaced, upon which the car vibrations returned to the normal level as shown in Figure 2.
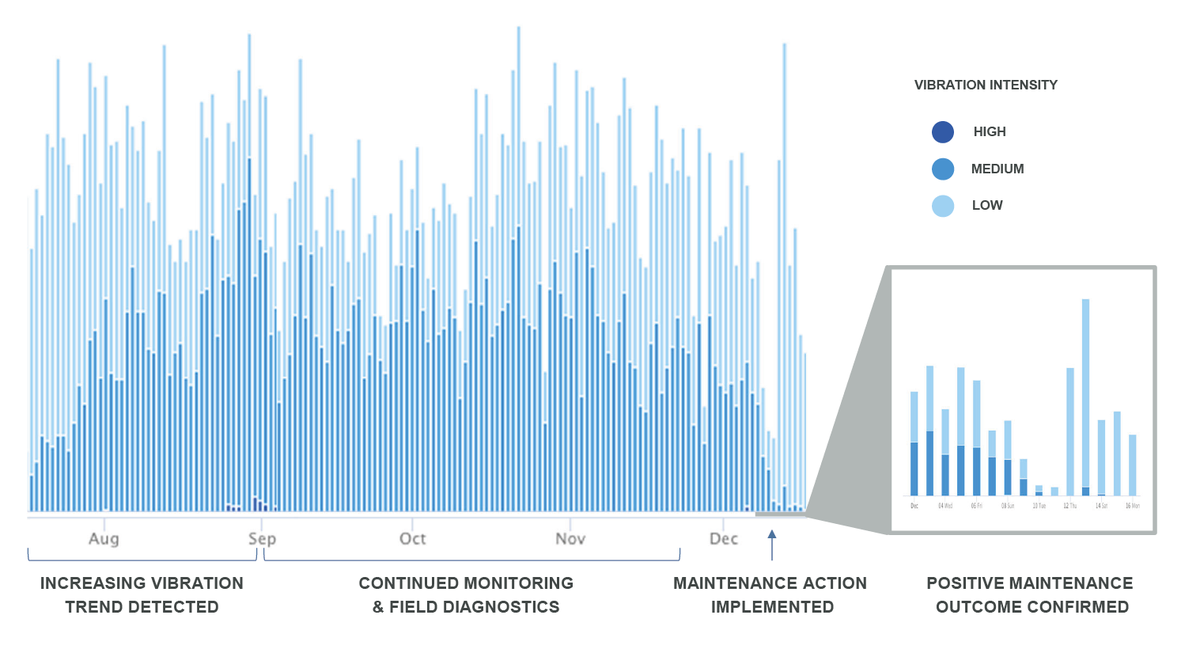
In many other cases, the CEDES Elevate team spotted increased vibration trends before the customer or the passengers did. Upon inspection, various issues such as dry rails or degrading counterweight rollers were reported and fixed before they could lead to an elevator breakdown, saving the customer time and money. And these are just ride comfort parameters.
Door issues are the leading cause of elevator breakdowns and generate anywhere between 60 to 80% of service callbacks. Therefore, measuring door performance is key to guiding targeted maintenance actions to improve equipment health and availability. In this case, a spike in car door vibration along with door closing times of over 4 seconds, out of the norm for that particular elevator, were identified. A technician was dispatched to check the car door on the third floor based on data from CEDES Elevate, where they found that the door operator bolts to the linkage arm had become loose. A quick change of hardware and proper tightening allowed for the issue to be resolved, and the elevator was kept in service. The building facilities team had no knowledge of the issue and were glad that the elevator company was able to act quickly and save a potential shutdown before it occurred.
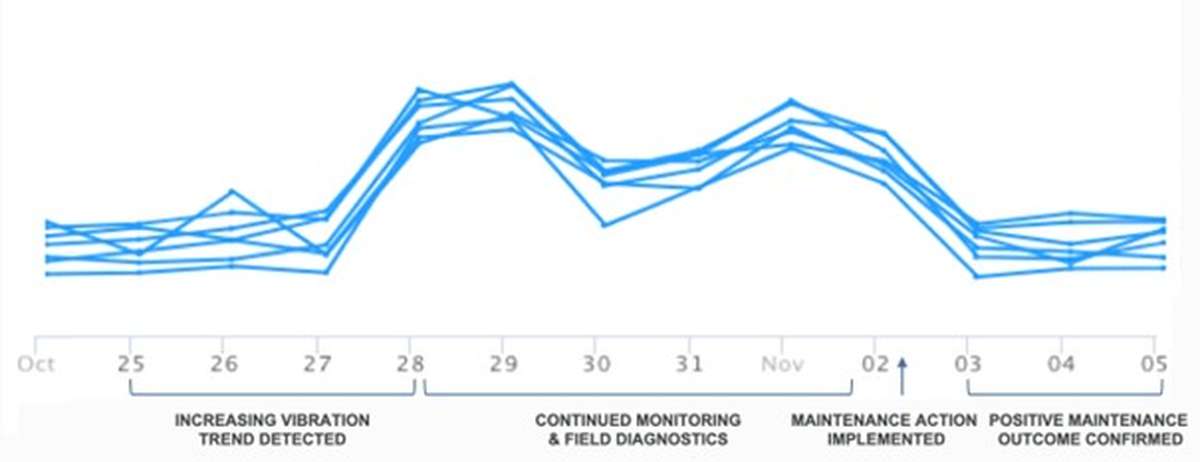
Additional features allow service companies to avoid other costly scenarios such as running on arrival. In this case, the real-time updates of the last ride time stamp would show that the elevator has self-recovered. This does not take away that in all likelihood there is an underlying issue that caused the initial breakdown to happen. However, being able to diagnose remote and the issue being less urgent means that fixing the root cause can now be planned and executed first time right, which means more control for the service provider. All in all, the unique feature set of CEDES Elevate aims to help service companies perform maintenance actions that are really needed, when they are needed.
Another great benefit of the solution lies in data transparency, with CEDES Elevate serving as the single source of truth and the basis for better reporting and compliance. A building owner in New York was complaining to the service company that their recently modernized elevator was too slow. Thanks to a detailed report on floor-to-floor speed from CEDES Elevate, the company was able to prove that the elevator actually met the speed rating specified in the contract (see Figure 4).
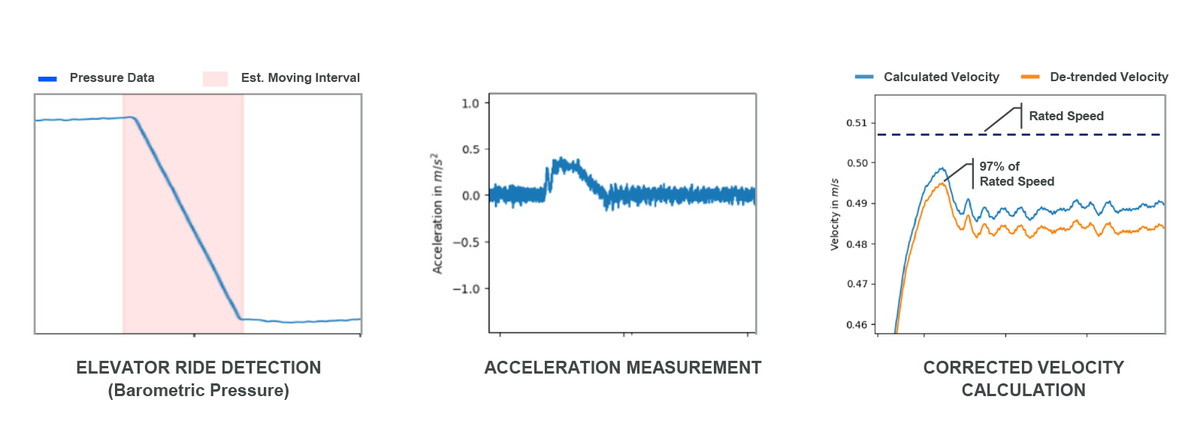
This example illustrates how real-time data insights can help service providers justify their actions, get their invoices paid and ultimately build more trust with their customers, resulting in lower churn rates.
Closing the Loop: Elevator Data Hub
The more data is gathered, the more informed decisions can be made. As a first step, we have added our 3D sensor for entrance area monitoring to the setup, in order to provide insights on elevator traffic on a per-floor basis, including the direction of the movement. Our goal is to create the ultimate elevator data hub - that is why CEDES has opened up its IoT platform for strategic partners. In cooperation with 2N, we combined IoT with code-compliant multimedia emergency communications, and the direct integration of data from Langer & Laumann’s door operators is under way.
The most recent partnership with FIELDBOSS has already generated massive interest. The planned joint solution will feed the CEDES Elevate insights directly into FIELDBOSS's advanced field service tools to trigger maintenance tickets and then circle back the information on completed maintenance back to CEDES Elevate – a complete closed-loop integration of IoT, data, service activities and then service outcomes. This is the turning point where data insights will automatically suggest actions in the field, allowing service companies to significantly streamline their operations, provide better maintenance, and upkeep safer elevators.
This article was first published in the Elevator World (February 2025).
To the top